Part 7 of my life in Wadi

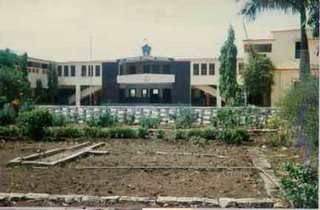
I got in touch with an old friend Dathathri today. He was an old timer of Wadi. His elder sister Rama was my classmate. He was my junior by one year in school. But let me not put the horse before the cart. Let me talk about the school first. The school in which I was studying, was called the St.Anne’s School by default as long as it was functioning from the Irani Building. But when it shifted to the new building that was built in ACC Colony, it was renamed St. Ambrose Convent School, ostensibly because the Bishop of the Diocese of Bellary at that time, under which the parish of Wadi fell, was The Rev. Dr. Ambrose Yeddanapally. We shifted to the building in 1973 when I was in 4th Standard. In Third standard, at St.Anne’s School in the Irani Building I was taught by one Fatima miss, whom I remember was in love with one Francis, Son of Arokiasamay, a civil overseer in ACC. I remember Arokiasamy as a dark fat man, who wore an English Hunter’s (Shikari type) hat, while he went about overseeing construction work in the ACC colony. They stayed in the quarter below us – at 31/11 at that time. Now this Francis was a young man who used to come to Irani building, stand outside the window and whistle while Fatima Miss was taking a class. Miss used to get all flustered and soon went out to meet Francis. Francis eventually joined ACC as a burner – or was it a Chemist?
Burner and Chemist are Technical terms for professionals engaged in certain types of works in a cement factory. Burners were responsible for keeping the output going, and chemists were responsible for the quality of the output. Both types were required to have a degree in chemistry but chemists were considered to be more elite. Chemists eventually became Chief Chemists and Burners became Chief Burners. It wouldn’t probably hurt a bit if I talked in brief about the cement making process a little at this stage and I copy from the Wikipedia the relevant parts. Thanx Wikipedia – I acknowledge you –
There are three fundamental stages in the production of Portland cement:
Preparation of the raw mixture
Production of the clinker
Preparation of the cement
The chemistry of cement is very complex, so cement chemist notation was invented to simplify the formula of common molecules found in cement.
The raw materials for Portland cement production are a mixture (as fine dust in the 'Dry process' or in the form of a slurry in the 'Wet process') of calcium oxide, silicon oxide, aluminium oxide, ferric oxide, and magnesium oxide. The raw materials are usually quarried from local rock, which in some places is already practically the desired composition and in other places requires the addition of clay and limestone, as well as iron ore, bauxite or recycled materials.
The raw mixture is heated in a kiln, a gigantic slowly rotating and sloped cylinder, with temperatures increasing over the length of the cylinder up to ~1480°C. The temperature is regulated so that the product contains sintered but not fused lumps. Too low a temperature causes insufficient sintering, but too high a temperature results in a molten mass or glass. In the lower-temperature part of the kiln, calcium carbonate (limestone) turns into calcium oxide (lime) and carbon dioxide. In the high-temperature part, calcium oxides and silicates react to form dicalcium and tricalcium silicates (C2S C3S). Small amounts of tricalcium aluminate (C3A) and tetracalcium aluminoferrite (C4AF)are also formed. The resulting material is clinker, and can be stored for a number of years before use. Prolonged exposure to water decreases the reactivity of cement produced from weathered clinker.
The energy required to produce clinker is ~1700 J/g. However, because of heat loss during production, actual values can be much higher. The high energy requirements and the release of significant amounts of carbon dioxide makes cement production a concern for global warming. Cement manufacturing emits 0.2 Pg C/yr as CO2. (1 Pg = 1 thousand million metric tons.)
In order to achieve the desired setting qualities in the finished product, about 2% gypsum is added to the clinker and the mixture is finely pulverized. The powder is now ready for use, and will react with the addition of water.
Francis and Fatima Miss married each other soon. Far as I remember they had no children. Why I mention this is that, love between a man and a woman was not really known to us while in third standard, and this perhaps, was the first exposure I and my classmates had in such affairs. Within a year or two we were to know all details about such things, though unlike students of elite public schools of today, we didn’t rush to experiment, but were content with developing theories on the subject. It was mostly a matter of mirth for all of us. We were 17 students in the class at this time, of which Rama was one. It was her brother Dathathri Naidu with whom I got in touch with today.
2 Comments:
there was one telugu couple living in 31/4. their children vijayanti the same class as deepa and his sister babu. pls give me the contact number or e-mail id of datha or santhanam. iyer uncle- engineer is at cochin. their son is an engineer. menon aunty has all the information of wadi families with her. i will try to get all the details from her. pls let me know if u want anything else
Greets to the webmaster of this wonderful site! Keep up the good work. Thanks.
»
Post a Comment
<< Home